Instrument services
Takara Bio is dedicated to helping our customers push their research to new frontiers with a comprehensive array of innovative technologies—from reagents to instruments. Our suite of instrument platforms enables the analysis of clinically relevant samples with high reproducibility while simplifying automation and high-throughput processing.
To help you achieve your research goals, we offer the following instrument service options:

IQ/OQ/IPV
Our Installation and Operational Qualification (IQ/OQ) and Instrument Performance Verification (IPV) service verifies and documents the instrument's ability to meet specified performance criteria after installation, repetitive use, or major service events. The IQ/OQ/IPV service involves comprehensive testing of the complete system using established conditions and known sample characteristics and provides a written report of the instrument performance.
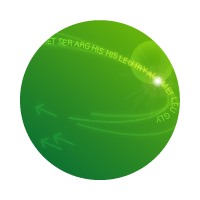
Installation
Prior to installation, we will send you a list of site preparation requirements needed for the smooth installation of your new instrument system. This list includes space requirements, power, and any user-supplied components. Once you have confirmed the site requirements are met, we will schedule a mutually suitable time for our Field Service Engineer (FSE) to install the system and perform initial qualification tests. Prior to the FSE leaving your site, we will provide you with a written confirmation that your system conforms to our specifications. The next step is for the Field Application Specialist to visit and provide hands-on training on how to use your system.
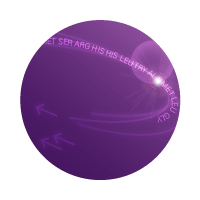
Training
Our certified Field Application Scientist (FAS) or Field Service Engineer (FSE) will visit your lab and provide one-on-one training on how to get the most from your instrument. The three- or five-day training (depending on the instrument purchased) includes best practices for general instrument operation as well as guidance on how to handle specific sample issues and advanced instrument operation. FAS/FSE training is specifically tailored to your system.

Preventative Maintenance
Preventative Maintenance (PM) is for the routine replacement of components that are expected to wear as an instrument is used in normal operation. After the instrument is serviced by our Field Service Engineers, the instrument will be qualified by conducting an Operational Qualification verification, and a written report will be provided. The price of each PM service includes all travel, labor, and replacement of normal wear and tear components but does not include replacement of parts that have failed from causes not associated with normal wear and tear.
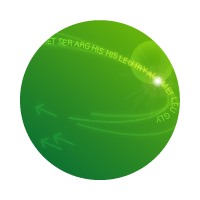
Service Plan
Service plans allow for customers to continue receiving maintenance and support for an instrument system beyond the expiration of the initial warranty. Single- and multi-year options are available. Service plans may be purchased while the instrument is under warranty. If the instrument is no longer under warranty, a repair service (at customer's expense) will be required before the Service Plan can go into effect. The price of each Service Plan includes one Preventative Maintenance visit and complete parts, labor, and travel for issues arising due to normal wear and tear.
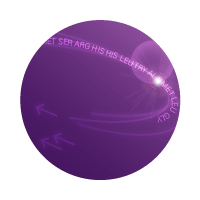
Repair
Repair service entails the replacement of parts that have failed unexpectedly and that are not expected to require replacement due to normal wear and tear.

Response time
Response time is defined as the time it takes for a certified Field Service Engineer to reach the customer site and begin repair work. Response time is guaranteed to be within five working days from notification.
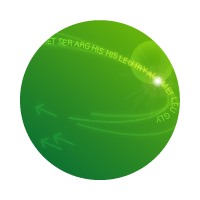
Warranty
A standard 12-month warranty is included with the purchase of every Takara Bio instrument system and covers all parts, labor, and travel for issues from normal instrument use. The warranty period begins either three months after shipment or after completion of initial Instrument Qualification, whichever is sooner.
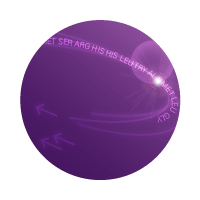
Instrument relocation
The instrument is prepared for travel, packed in an instrument-specific crate and moved to a new location. The instrument is then unpacked, installed on a workbench, preventative maintenance performed, a Re-Qualification-Operational Qualification/Instrument Performance Verification service is performed, and a written report provided. All work is completed by a certified Field Service Engineer.

A la carte options
The following services can be added to any service plan or purchased on an as-needed basis:
- Field Application Scientist/Field Service Engineer training is available at a quoted rate per day with travel and normal business expenses additional.
- Instrument relocation service with Re-Qualification-Operational Qualification/Instrument Performance Verification service included.
- Additional Preventative Maintenance visit is available for high-volume users—includes Operational Qualification report.
- Repair services are quoted depending on the specific circumstances.
Takara Bio USA, Inc.
United States/Canada: +1.800.662.2566 • Asia Pacific: +1.650.919.7300 • Europe: +33.(0)1.3904.6880 • Japan: +81.(0)77.565.6999
FOR RESEARCH USE ONLY. NOT FOR USE IN DIAGNOSTIC PROCEDURES. © 2025 Takara Bio Inc. All Rights Reserved. All trademarks are the property of Takara Bio Inc. or its affiliate(s) in the U.S. and/or other countries or their respective owners. Certain trademarks may not be registered in all jurisdictions. Additional product, intellectual property, and restricted use information is available at takarabio.com.